Dad Discarded Mom for Someone Younger—I Took Revenge
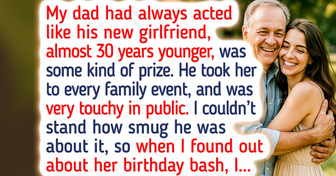
To build an underwater structure, you’ll need some interesting engineering. A large bridge over a river or bay has its foundation rooted underwater. It’s even more complicated with undersea tunnels. Underwater construction is challenging. Engineers need to deal with water pressure and corrosion from saltwater. There’s also a problem of finding suitable materials.
The most typical of them are concrete, steel, and acrylic glass. Concrete doesn’t care about water currents and doesn’t get damaged by saltwater. Steel provides underwater constructions with a strong structure. And acrylic glass is tough, long-lasting, and resistant to sunlight. It’s also transparent, that’s why it’s often used to make windows in underwater buildings. Anyway, when the water is shallow, it’s not that hard to build something there. Constructors create a temporary foundation. Then, on top of it, they build several piers supporting the upper structure.
But if the waters are deep, engineers have to use other methods. Depending on which one they choose, water is either extracted or diverted during the construction process. One of such methods involves using a set of large driven piles. Those are long, thin columns made mostly of steel. But their interior is partially hollow. With the help of a huge hammer, they get driven into the waterbed, like nails are driven into a piece of wood.
After that, these steel columns get filled with concrete through a special tube. The concrete displaces the water that was in the pile before. Concrete has the ability to set even when it’s surrounded by water. That’s why driven piles eventually turn into a stable foundation for overwater and underwater constructions. Driven piles are a very cost-effective way of building something that has to be fixed in place. They prevent things from being moved by the water current.
Another way to build underwater structures is cofferdams. They are built temporarily and allow workers to create a dry space for the construction. The water gets pumped out of this enclosure, and the cofferdam works like a dam. A completed cofferdam looks like a massive pit with high walls surrounded by water. Cofferdams are made of rocks, steel, and even dirt. These constructions can be built fast and removed even faster. But the process of putting up a cofferdam is complicated and challenging for engineers. They have to make sure the structure won’t flood or collapse.
The simplest way to build a cofferdam is to pile up loads of dirt. But in this case, workers usually have to somehow make the construction stronger. It helps to protect it from the damage caused by water. Once the cofferdam is ready, pumps extract the water from its interior. Sometimes, it’s too expensive to build a very deep and strong cofferdam. In this case, constructors use several powerful pumps that get rid of excess water when it seeps through the cofferdam walls.
If a cofferdam starts to fail, this process is slow and, luckily, predictable. On the construction site, there are not only main but also backup pumps. In case of emergency, they can kick into overdrive. Then, the water is kept out for the time the personnel needs to evacuate. Cofferdams are most often used during the construction of dams and bridges. But when a large ship (like a modern cruise liner) needs to be repaired, engineers use cofferdams too. Such vessels are too massive to be hauled ashore. And a cofferdam makes a perfect dry lock. The ship gets isolated from the water, and mechanics can repair it wherever it sits.
Also, when a cruise ship needs to be expanded, engineers construct a cofferdam around it. Then they pump out all the water from the inside, creating a dry working place. The ship gets cut into two parts, and the process of its lengthening begins. There are several main types of cofferdams: braced, cellular, rock-filled, or earthen. For each of them, engineers need to figure out the best depth at which the wall should be put into the ground. It depends on the type of soil and the water reservoir itself.
Braced cofferdams are mostly used during shallow-water construction. Such a structure is actually a wall of sheet piles. Those are parts with interlocking edges. Usually, they are made of steel. But the material can also be reinforced concrete or timber. Sheet piles create something like a box around the needed area.
Cellular cofferdams are also made of sheet piles. But in this case, the piles have a special shape. After being connected, they form cells that get filled with soil or clay. The cells, in turn, create a watertight wall. Thanks to its structure, it’s exceptionally stable.
Rock-filled cofferdams are used when there’s a lot of rock at the construction site. They’re built over the soil. This prevents the water from seeping into the cofferdam. And the rocks serve as reinforcement.
Earthen cofferdams are built in areas where the water is less than 10 ft [3m] deep. They are created from the materials that are at hand: clay, sand, even soil! There are also single-walled and double-walled cofferdams.
The first type is used when the area of the construction isn’t large, and the depth is more than 20 ft [6 m]. Such cofferdams are typically necessary for building bridges. Timber or wooden sheets are put into the sea or river bed. After that, iron or steel sheets are added on the inside. On both sides of the wall, workers place half-filled bags of sand. Finally, the water gets pumped out, and the cofferdam is ready for use.
The double-walled cofferdam is used for large construction areas, and when the water is very deep. Such construction sites need more powerful supports. This stronger cofferdam has two walls, which provides it with extra stability. Two piles get pushed into the water bed with some space in-between. (The deeper it is, the bigger the space between the walls.) Then they get attached to each other. After that, this space gets filled with soil.
Cofferdams aren’t cheap. This means that if one is used for a project, there are no other available options. For example, it’s the best way to construct permanent dams. When the Hoover Dam was built, several cofferdams were put up to divert the water from the Colorado River. As soon as the project is finished, the water is pumped back into the cofferdam. And its walls (whatever they are) get removed.
One more way of underwater construction is caissons. They’re watertight structures that are put into the water. Even open, they remain dry inside. Workers can keep digging down until they reach some solid surface. That’s where the caisson will be placed upon. What’s so different about caissons is that they eventually become parts of the foundation for, let’s say, a bridge or a dam.
And even though you might not think of a bridge or a dam as an “underwater construction,” most of their crucial elements are underwater. For example, a large bridge wouldn’t be able to hold its weight without massive supporting towers. And they stand in the water. There are several types of caissons: open, pneumatic, and box. Open caissons have no bottom. They’re actually just vertical walls that allow builders to dig at the bottom of them.
Pneumatic caissons keep the water from seeping through by using compressed air. This helps to maintain equal pressure inside and outside the construction. When workers dig out some materials, these get sent up through a special muck tube. When the caisson reaches the bedrock, workers fill it with concrete. Unlike others, a box caisson has a floor. And workers lower it onto a foundation that is constructed in advance.
During the construction of the Brooklyn Bridge, engineers used two massive caissons. Thanks to them, they reached the bedrock and created the foundation for the towers of the bridge. And then, there’s also off-site construction. That’s when things are not only built but also assembled away from the site. In this case, engineers often use modular construction. That’s when factory-produced building units are delivered to the site. There, they get assembled, like a giant Lego set.
Structures are then usually floated to the site on huge barges. Or they get towed there. After that, they’re lowered in place. Some sink under their own weight. Others can only reach the seafloor after getting loaded with additional weights. This method of construction is rather expansive. And still, it’s much more cost-effective than building right underwater. The latter needs skilled engineers and unique tools. And don’t forget about the risks!
But what about underwater tunnels? How on Earth are they constructed?! Modern tunnels are usually built with the help of massive tunnel-boring machines. They have a nickname — “moles.” Even though such a mechanism has an exorbitant price (several millions of dollars), it needs little time to create a long tunnel. The machine moves forward very slowly. It has a special circular plate with rotating disk cutters. They can easily chew through solid rock. The rock is then dropped onto an outbound conveyor belt. Another mechanism uses this rock to construct the tunnel lining in the “mole’s” wake.
This way, the “mole” not only excavates the tunnel but also reinforces the walls that will later support it. This method (and 11 huge tunnel-boring machines) was used to build the 32-mile-long Channel Tunnel. And the whole process took only three years. Cut-and-cover is another method of creating a tunnel underwater. First, workers dig a trench in the ocean floor or riverbed. Then they put there concrete or steel tubes there made in advance. After the tubes get covered with a thick layer of rock, the sections are connected. All workers have to do is to pump out the water.
That’s how the Ted Williams Tunnel, connecting Logan Airport with South Boston, was built. There, they used 12 enormous steel tubes, more than 300 ft [91 m] each. And the tubes contained already fully constructed roads!